Composition and use instructions of high alumina refractory cement for refractory casting
Jun 10, 2022
High alumina cement also refers to cement with calcium aluminate as the main component. Mainly calcium aluminate, clinker with alumina content of about 50%, ground hydraulic cementitious material, called high alumina cement. Calcium aluminate cement is a basic binder for unshaped refractories, especially cast refractories, and is rarely used in the production of refractory bricks.
The chemical composition of high alumina cement is mainly Al2O3 and CaO, and some also contain a considerable amount of Fe2O3 and SiO2. The mineral composition consists of the following five minerals: monocalcium aluminate CaO·Al2O3 (CA), calcium aluminate CaO·2Al2O3 (CA2), dodecalumina heptaaluminate 12CaO·7Al2O3 (C12A7) three compounds and inclusions. It is composed of calcite 2CaO·Al2O3·SiO2 (C2AS), tetra calcium ferric aluminate 4CaO·Al2O3·Fe2O3 (C4AF), etc.
The properties of aluminate cement are mainly determined by its mineral composition. The main mineral composition of aluminate cement is monocalcium aluminate (CA), which has high hydraulic activity. Although the setting is not very fast, it hardens rapidly (hardening time does not exceed one day), which is the main strength of high alumina cement, especially the early strength. source. Calcium aluminate (CA2) hydrates and hardens slowly, with lower early strength and higher late strength. Dodecacalcium heptaaluminate (C12A7) has the characteristics of rapid hydration and rapid condensation, but the strength is not high. In ordinary high-alumina cement containing inclusions (calcite feldspar C2AS, tetra calcium ferrite C4AF), C4AS plays a role in hardening the cement as soon as possible, while in advanced high-alumina cement, C12A7 plays a hardening role. As for C2AS basically does not produce hydration, it cannot show its strength.
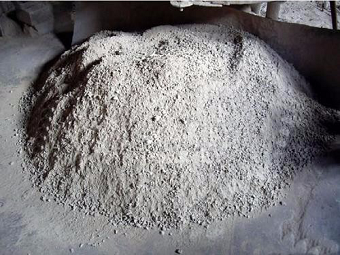
Calcium aluminate cement contains 5 kinds of calcium aluminate minerals, and these calcium aluminates will show an intense heating phenomenon with the progress of the hydration reaction. Ordinary high alumina cement (53~55%Al2O3) reaches its peak temperature at 5~8h thickness, up to 80~90ºC; 70%Al2O3 high alumina cement is 10~12h thick, and 80%Al2O3 advanced high alumina cement is 8~90ºC. After 10h, the temperature reached its peak value at 80ºC and 70ºC, respectively.
The heating temperature and the time to reach the highest temperature of different types of high alumina cement single cast body are determined by the heating characteristics and content of calcium aluminate contained.
Fast-hard C12A7 and C4AF generate higher heat. Therefore, the calorific value of high alumina cement will also vary depending on the aluminate content. If too much high alumina cement containing C12A7 or C4AF as the main component is added to the castable refractory, the concentrated heat will cause the water in the hardened body of the castable to evaporate violently and cause cracks and surface peeling. Therefore, it is very important to choose the amount and quality of cement.
High alumina cement transportation and storage
During the transportation and storage of aluminate cement, special attention should be paid to moisture-proof to prolong the storage period and avoid affecting the performance of the product;
During transportation, storage, and use of aluminate cement, avoid contact with other types of cement (such as Portland cement, etc.) and harmful impurities (such as lime, etc.);
During the use of aluminate cement, the mixing water should be pure, so as to avoid possible harmful impurities that may affect the performance of the product.
Relevant information
-
Main properties of magnesium oxide refractory
Performance characteristics of magnesia refractories and other basic refractories Performance characteristics of magnesia refractories and other basic refractories Refractories containing more than 80% ... -
What properties of lightweight insulation fire clay bricks can be improved by the addition of kyanite?
Lightweight insulation fire clay bricks are a kind of shaped refractory material with clay as the main raw material, which is processed, shaped, dried, and calcined with clay. on the kiln. Due to the r ... -
How is the effect of white fused alumina abrasive used in refractory materials?
After mixing, forming, drying, and firing at high temperature in a shuttle kiln. The product has the characteristics of high refractoriness, good thermal shock stability of white corundum, high high te ... -
Characteristics of refractory magnesia chrome bricks for lime kiln
Lime kilns are mainly classified into square kilns and circular kilns. According to the classification of fired products, they can be divided into lime kilns, ceramic kilns, cement kilns, glass kilns, ...