Selection basis of raw materials for preparing high alumina firebrick
May 26, 2022
Selection of a binding agent
The manufacture of high alumina firebrick usually uses soft clay as a binder. The main function of clay in the batching is to improve the molding properties of the clay and make the green body after molding and drying have a certain strength. However, during the sintering process, the free SiO2 in the clay and the free A12O3 in the high alumina bauxite clinker undergo a secondary mulliteization reaction, which intensifies with the increase of the amount of bound clay added. The stronger the secondary mullite reaction, the higher the porosity of high alumina bricks after firing, and the greater the possibility of decreasing strength and bulk density. From this point on, the amount of bound clay added to the ingredients should be minimized. The amount of clay powder added to the ingredients is generally 5%.
In order to obtain volume-stable Xia and another high alumina firebrick, high alumina bauxite powder can be used as a high alumina binder; Volume-stable high alumina firebrick without secondary expansion can be prepared.
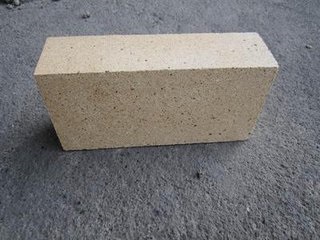
Determination of particle composition
The particle composition of high-alumina bauxite clinker has an important influence on forming operation, green body density, high alumina firebrick density, and strength. Therefore, determining a reasonable particle composition according to different molding methods is an important process factor to stabilize the process operation and improve the quality of the high alumina firebrick.
The principle of determining particle gradation is to form a good bulk density, which has no adverse effect on the performance and appearance quality of high alumina firebrick. For bricks such as Xia, the volume expansion caused by the secondary mulliteization reaction should also be considered.
High alumina firebrick usually uses coarse, medium, and fine three-level ingredients. However, secondary or quaternary ingredients may also be used. When three grades of ingredients are used, the critical size of each grade is 3-0.5mm for coarse particles, 0.5-0.1mm for medium particles, and <0.1mm for fine powder.
In short, to determine a reasonable particle ratio, it is necessary to consider a reasonable bulk density and limit the number of intermediate particles added; but also to determine the critical size and the number of particles added at all levels according to the different molding methods; and the performance and requirements of high-alumina bricks. In the general brick-making process, the upper limit of coarse particles is usually 2-3mm, and the addition amount is 40-45%. For special-shaped high alumina firebrick, the upper limit of coarse particles can be reduced to 1-2mm. The number of intermediate particles of 1-0.1mm should be limited to 10-20%; the amount of fine powder <0.1mm should be controlled at 40-50%.
Relevant information
-
Main properties of magnesium oxide refractory
Performance characteristics of magnesia refractories and other basic refractories Performance characteristics of magnesia refractories and other basic refractories Refractories containing more than 80% ... -
What properties of lightweight insulation fire clay bricks can be improved by the addition of kyanite?
Lightweight insulation fire clay bricks are a kind of shaped refractory material with clay as the main raw material, which is processed, shaped, dried, and calcined with clay. on the kiln. Due to the r ... -
How is the effect of white fused alumina abrasive used in refractory materials?
After mixing, forming, drying, and firing at high temperature in a shuttle kiln. The product has the characteristics of high refractoriness, good thermal shock stability of white corundum, high high te ... -
Characteristics of refractory magnesia chrome bricks for lime kiln
Lime kilns are mainly classified into square kilns and circular kilns. According to the classification of fired products, they can be divided into lime kilns, ceramic kilns, cement kilns, glass kilns, ...