Production process of direct bonded magnesia-chrome brick for cement kiln
May 05, 2022
Directly bonded magnesia-chrome bricks refer to refractory products that are directly combined with periclase and magnesia-chrome spinel as the main crystal phases. The brick is made of high-purity sintered magnesia and chromite with SiO2 less than 2% by high temperature sintering. Direct bonding refers to a bonding produced by direct contact between solid-phase grains. The brick is made of high-purity sintered magnesia and chromium concentrate with SiO2<2% as raw materials, and is sintered at high temperature. The degree of direct bonding of the product increases with the decrease of SiO2 content and the increase of sintering temperature.
Introduction of direct bonded magnesia-chrome brick for cement kiln
Directly bonded magnesia-chrome bricks refer to refractory products that are directly combined with periclase and magnesia-chrome spinel as the main crystal phases. The brick is made of high-purity sintered magnesia and chromite with SiO2 less than 2% by high temperature sintering.
Direct bonding refers to a bonding produced by direct contact between solid-phase grains.The degree of direct bonding of the product increases with the decrease of SiO2 content and the increase of sintering temperature.
Performance of direct bonded magnesia-chrome brick for cement kiln
The product has few impurities. After high temperature and ultra-high temperature firing, the glass phase is concentrated in the triangular area of the crystal phase, and the crystal phase and the crystal phase are directly combined. It has low porosity, high compressive strength, strong wear resistance, corrosion resistance, thermal shock resistance and good spalling resistance [2] .
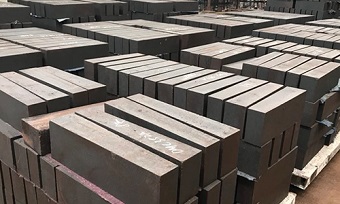
Application of direct bonded magnesia-chrome brick for cement kiln
Directly combined with magnesia-chrome bricks are widely used in electric arc furnaces, copper smelting converter flash furnaces, RH, DH vacuum treatment devices, out-of-furnace refining VOD furnaces, AOD furnaces, cement rotary kilns, etc.
Production process of direct bonded magnesia-chrome brick for cement kiln
In order to form a direct bond, the SiO2 content of the raw material should be low, and the firing temperature must be increased. The SiO2 content of the existing directly bonded magnesia-chrome bricks is generally less than 2%, and the firing temperature is between 1700 and 1800 °C. The formation of direct bonds is a dissolution-precipitation process. Increasing the fine powder content of the chrome concentrate is conducive to the formation of direct bonds. Therefore, attention must be paid to the proportion of chromium concentrate fine powder in the ingredients. In the presence of silicates, the bond between periclase and periclase will be strengthened by Cr2O3, and reduced by Al2O3 and Fe2O3. Adding Al2O3 or Fe2O3 to magnesia-chrome bricks can reduce the melting point of silicates, while adding Cr2O3 will reduce the melting point of silicates. Raise the melting point. Therefore, chrome ore with high Cr2O3 content has higher high temperature strength than chrome ore with low Cr2O3 content. Secondary spinel is characteristic of direct bond bricks. The higher the Cr2O3 content, the more intragranular and intergranular spinels, the higher the product strength and the stronger the slag resistance.
Relevant information
-
Main properties of magnesium oxide refractory
Performance characteristics of magnesia refractories and other basic refractories Performance characteristics of magnesia refractories and other basic refractories Refractories containing more than 80% ... -
What properties of lightweight insulation fire clay bricks can be improved by the addition of kyanite?
Lightweight insulation fire clay bricks are a kind of shaped refractory material with clay as the main raw material, which is processed, shaped, dried, and calcined with clay. on the kiln. Due to the r ... -
How is the effect of white fused alumina abrasive used in refractory materials?
After mixing, forming, drying, and firing at high temperature in a shuttle kiln. The product has the characteristics of high refractoriness, good thermal shock stability of white corundum, high high te ... -
Characteristics of refractory magnesia chrome bricks for lime kiln
Lime kilns are mainly classified into square kilns and circular kilns. According to the classification of fired products, they can be divided into lime kilns, ceramic kilns, cement kilns, glass kilns, ...