Development of refractory lightweight high alumina brick
Apr 18, 2022
Refractory lightweight high alumina brick is one of the ideal heat-insulating refractory materials at present. It has the characteristics of high compressive strength, low thermal conductivity, good heat preservation performance, and low price. It is widely used in ceramic tunnel kilns, rod kilns, and shuttle kilns. , wall kiln, various heating furnaces, coke ovens and other thermal equipment, heat treatment pipelines in the steel industry. The refractory lightweight high alumina brick developed and produced have high temperature, delicate materials, unique production process, low cost, excellent product performance, and quality, and short development time.
1. Raw material requirements
a. Clinker: crushed by a wheel defect machine, crushed by a vibrating ball mill, passed through a 4-mesh sieve (coarse particle) and an 80-mesh sieve (fine particle), and then stored in the warehouse for future use. Particles: medium particles: fine particles = 5:2:3 match.
b. Kaolin: hand-selected third-grade Suzhou clay, its chemical composition is Al2O3>34%; Si02<49%; Fe203<0.5; CaO+MgO<1.5; K20+Na20<0.5.
c. Industrial alumina: produced by Henan Zhengchuan Alumina Plant, its chemical composition is: Al2O3> 99%; Fe2O3 <0.05%; Si02<0.10%.
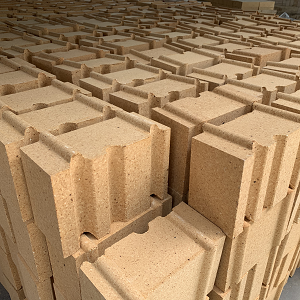
2. Preparation of Foaming Agent
The materials used to prepare the foaming agent are caustic alkali, rosin, and bone glue. First, the caustic alkali and water are heated in a water bath in proportion to be completely dissolved, and the rosin powder (not larger than 3 mm) is slowly added to the caustic alkali and water solution. After all the reactions are galvanized, bone glue (swelling glue block soaked in water) is added. Under vigorous stirring (about 80 ℃), it is fully mixed into a viscous concentrated foaming agent, dried and broken, with a pore size range of 161 pores/cm2.
3. Ingredients
First, add the raw material, industrial alumina, and Suzhou soil into the mixing tank for two minutes, then add the foaming agent and the binder, and stir while stirring. After stirring, the material can be used for 24 hours.
4. Forming and drying
Lightweight high alumina brick using high-frequency vibration pressure forming, first, add raw materials, and control the weight. When forming, the key is to adjust the pressure and time, otherwise, the extruded bricks will be layered, and the foaming agent will be concentrated on the upper layer, which will easily cause surface defects after burning. The formed semi-finished products are transported to the drying room, where they are dried at 40°C for 24 hours and at 60°C for 24 hours.
5. Firing
The bricks are fired in a domestic 24-meter gravity center tunnel kiln, the temperature is controlled at 1420-1470't:, and the firing cycle is 24 hours.
Relevant information
-
Main properties of magnesium oxide refractory
Performance characteristics of magnesia refractories and other basic refractories Performance characteristics of magnesia refractories and other basic refractories Refractories containing more than 80% ... -
What properties of lightweight insulation fire clay bricks can be improved by the addition of kyanite?
Lightweight insulation fire clay bricks are a kind of shaped refractory material with clay as the main raw material, which is processed, shaped, dried, and calcined with clay. on the kiln. Due to the r ... -
How is the effect of white fused alumina abrasive used in refractory materials?
After mixing, forming, drying, and firing at high temperature in a shuttle kiln. The product has the characteristics of high refractoriness, good thermal shock stability of white corundum, high high te ... -
Characteristics of refractory magnesia chrome bricks for lime kiln
Lime kilns are mainly classified into square kilns and circular kilns. According to the classification of fired products, they can be divided into lime kilns, ceramic kilns, cement kilns, glass kilns, ...