Construction and application of high alumina castable refractory
Apr 02, 2022
With the continuous increase of blast furnace hot air temperature, higher requirements are put forward for high-alumina castables' high-temperature creep performance, thermal shock stability performance, load softening temperature, etc. According to the investigation, a high-strength, non-shrinking high-alumina castable was developed on the basis of the original high-alumina castable, and its formula was adjusted as follows:
(1) The use temperature of the castable is above 1400 °C, and a certain raw material must be added to offset the high temperature shrinkage performance of the product through a high temperature reaction.
(2) Adding metal silicon powder during high-temperature use of castables can completely solve the drawbacks of high-temperature shrinkage, offset its high-temperature creep, and reduce shrinkage cracks during high temperature use. Its addition effect is better than kyanite and andalusite.
(3) The addition of silicon metal in the castable is 1%, and the product can have better high temperature performance, especially shrinkage resistance.
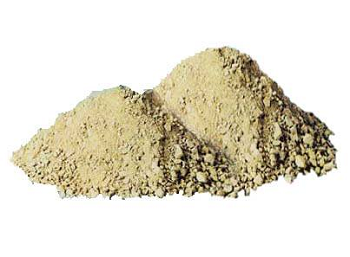
Construction and Application
1. Pouring construction
Put the material into the double-shaft forced mixer, dry mix for 1~2min, control the water amount of 5%~5.5%, add 90% of the water amount first, and adjust the water amount according to the season and construction environment, but the water amount should not be added. Beyond the control range, increased moisture will reduce strength and performance. Pour the material into the mold, and vibrate it with a vibrating rod while feeding. It requires vibrating. Each batch of 500kg is completed within 6 minutes. The interval between batches should not exceed 6 minutes, and the interval should be shortened as much as possible to prevent product delamination.
2. Demoulding and baking
The demoulding time can be 24 hours in spring and autumn, and 8 hours in summer. In winter, it should be formed on sunny days (larger construction bodies are generally formed outdoors). It is suitable to extend the demoulding time to about 1 day, to prevent the products from being frozen. Prevent the generation of surface mesh cracks. The baking temperature is above 200℃.
3. Use effect
High-strength, non-shrinking, and high-alumina castables are used in blast furnaces, rotary kilns, heating furnace tops, sintering machine igniters, and other parts.
Relevant information
-
Main properties of magnesium oxide refractory
Performance characteristics of magnesia refractories and other basic refractories Performance characteristics of magnesia refractories and other basic refractories Refractories containing more than 80% ... -
What properties of lightweight insulation fire clay bricks can be improved by the addition of kyanite?
Lightweight insulation fire clay bricks are a kind of shaped refractory material with clay as the main raw material, which is processed, shaped, dried, and calcined with clay. on the kiln. Due to the r ... -
How is the effect of white fused alumina abrasive used in refractory materials?
After mixing, forming, drying, and firing at high temperature in a shuttle kiln. The product has the characteristics of high refractoriness, good thermal shock stability of white corundum, high high te ... -
Characteristics of refractory magnesia chrome bricks for lime kiln
Lime kilns are mainly classified into square kilns and circular kilns. According to the classification of fired products, they can be divided into lime kilns, ceramic kilns, cement kilns, glass kilns, ...