Low creep fire clay brick price
Apr 27, 2022
Low-creep fire clay bricks are made of coke gemstone clinker with dense structure, high initial degree, and few impurities as the main raw material, and some synthetic mullite and kyanite raw materials are added to form mud material, which is formed by high pressure, dried and fired at high temperature. It is suitable for thermal equipment such as blast furnaces, hot blast furnaces, ladle lining and casting, iron furnaces, heating furnaces, glass melting furnaces, boilers, and coke ovens.
The low creep fire clay brick is a further improvement of the ordinary fire clay brick production process, mainly to meet the requirements of the working environment of the blast furnace, and the large-scale blast furnace puts forward higher requirements for the blast furnace hot blast stove air temperature. Due to the increase in air temperature, the requirements for fire clay bricks for hot blast stoves have also increased, requiring better high-temperature volume stability, creep, and wear resistance. Therefore, all ordinary fire clay bricks produced with clay raw materials can no longer meet the requirements of high air temperature and hot air, and it is necessary to produce fire clay bricks with low creep. The raw materials for low-creep fire clay bricks must be dense in structure, high in purity, and low in impurities, so as to avoid excessive liquid phase during firing and reduce creep resistance. It also has excellent thermal shock resistance and erosion resistance.
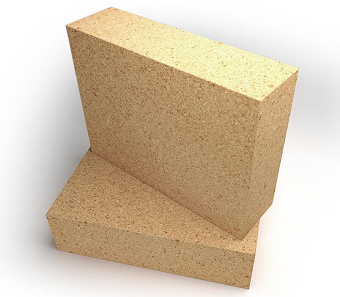
Low creep fire clay brick product characteristics
(1) Strong volume stability at high temperature.
(2) High refractory temperature.
(3) The creep rate at high temperatures is small.
(4) High strength and strong wear resistance.
(5) Resistant to chemical attack.
(6) Excellent thermal shock resistance.
The application fields of low creep fire clay bricks are quite extensive, but with the expansion of kiln scale, the technology of refractory materials is constantly updated, and the fierce market competition urges the research and development of new refractory products, such as low creep high alumina bricks. fire clay bricks are made of clay (including shale, coal gangue, and other powders) as the main raw material, which is processed, shaped, dried, and roasted with mud. There are solid and hollow. fire clay bricks have a long history, and improvements over the years have made the performance of fire clay bricks even better. According to the porosity rate: solid bricks (bricks with no holes or less than 25% porosity), porous bricks (the porosity rate is equal to or greater than 25%), bricks with small holes, and a large number of bricks are often used in load-bearing parts and have higher strength levels. high. Hollow bricks (bricks with porosity equal to or greater than 40%, large size and a small number of holes, often used in non-load-bearing parts, with low strength grade). When we choose refractory materials, we have considered many aspects to choose suitable refractory brick products.
Relevant information
-
Main properties of magnesium oxide refractory
Performance characteristics of magnesia refractories and other basic refractories Performance characteristics of magnesia refractories and other basic refractories Refractories containing more than 80% ... -
What properties of lightweight insulation fire clay bricks can be improved by the addition of kyanite?
Lightweight insulation fire clay bricks are a kind of shaped refractory material with clay as the main raw material, which is processed, shaped, dried, and calcined with clay. on the kiln. Due to the r ... -
How is the effect of white fused alumina abrasive used in refractory materials?
After mixing, forming, drying, and firing at high temperature in a shuttle kiln. The product has the characteristics of high refractoriness, good thermal shock stability of white corundum, high high te ... -
Characteristics of refractory magnesia chrome bricks for lime kiln
Lime kilns are mainly classified into square kilns and circular kilns. According to the classification of fired products, they can be divided into lime kilns, ceramic kilns, cement kilns, glass kilns, ...