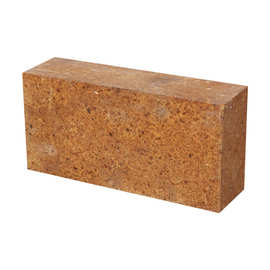
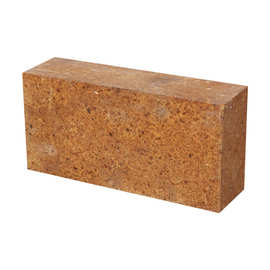
Refractory magnesia alumina brick for glass kiln
Model Number: Hongtai
Certification: IS09001
Minimum Order Quantity: 1 ton
Refractory magnesia alumina brick for glass kiln
The magnesia-alumina brick is made of ordinary sintered magnesia and high-alumina bauxite clinker. The magnesia-alumina spinel mineral is formed in the matrix of the brick during the firing process.
The glass kiln is a high-temperature melting furnace, which needs to run continuously for 8 to 15 years. The matching regenerator is the passage of combustion-supporting air and exhaust gas in the normal operation of the glass kiln, so it is necessary to ensure a good use effect. The maximum temperature of the regenerator can reach 1450 ℃ ~ 1550 ℃, the fly material in the glass kiln is easy to stick to the surface of the refractory material, and the refractory material is easy to be blocked, which leads to the damage of the structure.
Magnesium refractory has the advantages of high melting point and excellent corrosion resistance, and is suitable for use in parts with severe alkali erosion at high temperature. In order to improve the service life of the regenerator of the glass kiln, magnesia refractories with Mg0≥97% are mostly used in the middle and upper parts of the regenerator to prepare magnesia refractories. The existing production process of high-purity magnesia bricks for glass kilns uses natural first-grade or special-grade magnesite as raw materials, and high-purity magnesia obtained by light firing, briquetting, and high-temperature shaft kiln sintering as the main raw materials, and the binder uses sulfate-containing materials.
The pulp waste liquid or pulp dry powder is then fired at a temperature of 1750 ℃ in an ultra-high temperature tunnel kiln. Since the binder contains sulfate, sulfur-containing oxides are inevitably generated after high-temperature sintering, which will adversely affect the environment. With the continuous mining of magnesite resources, the resources of high-grade first-grade magnesite and super-grade magnesite gradually decrease, which leads to the decline of the overall quality of magnesia raw materials, which brings difficulties to the manufacturing process of high-purity magnesia bricks for glass kilns. With the development of beneficiation technology, the use of low-grade tertiary ore for flotation to obtain high-grade magnesite
Mining technology is gradually developed. The magnesite is purified by the combined process of reverse flotation, and then high-purity magnesia is obtained by light burning and heavy burning. The magnesia raw material Si0 obtained by the flotation process can be as low as 0.3wt%, and the Mg0 content can reach 97.5wt%
The above provides a raw material basis for the preparation of high-performance magnesia bricks for glass kilns.
As a high-temperature industry, the refractory industry will focus on carbon peaking and carbon neutralization. The production process of refractory materials requires technological progress and energy saving and consumption reduction. At present, the sintering temperature of magnesia refractories is high, especially the sintering temperature of high-purity magnesia bricks is 1750℃~1810℃, which consumes a lot of energy; the thermal shock resistance (950℃, air quenching) of the obtained magnesia refractories is about 8 times . Under the dual carbon target, the service life of the glass furnace is required to be at least 8 years. This requires R&D to save High-performance magnesia bricks with energy and an environmentally friendly manufacturing process and a longer service life.
Application
Used for steelmaking open hearth and electric furnace, glass kiln, refractory products firing tunnel kiln, shuttle kiln and other kilns.
Production capacity: Our factory actively response to government environmental protection policy, we designed and built the fully automatic controlled high temperature gas tunnel kiln (1700℃), and got capacity of annual output 70,000 tons of high quality refractory products.
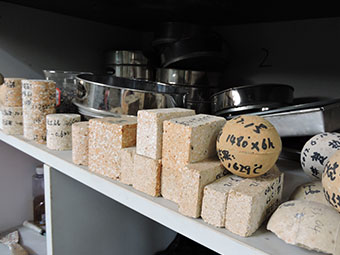
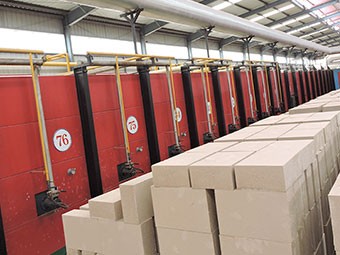
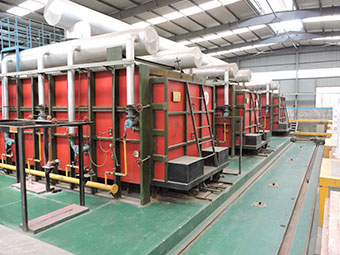
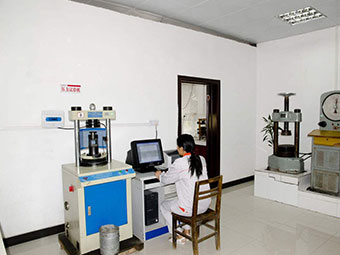
Packing details:
★Bricks: Fumigated wooden pallet with log paperboard covered and stainless steel band strapping, the whole outside is wrapped with thermoplastic film. Or carton packaging.
★Wooden pallet size: usually 92*92cm (standard brick)
★Castable: Ton bag with rain film and 25kg bags inside
★Or according to customer’s requirements
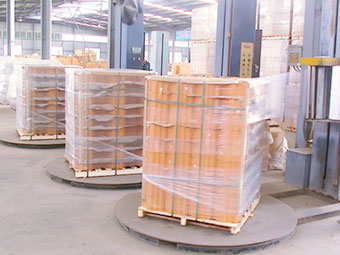
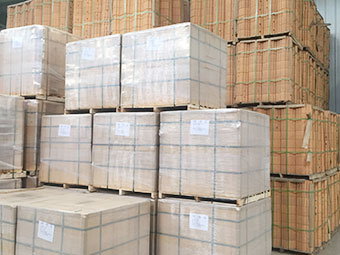
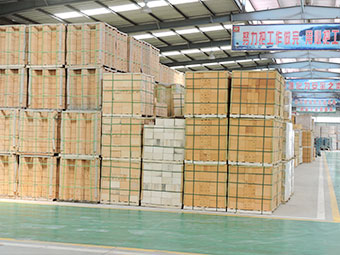
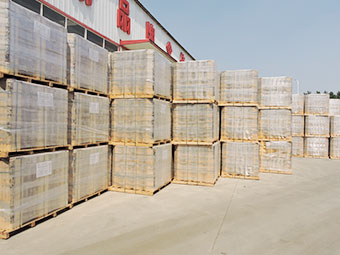
Transportation
★Port of dispatch: Tianjin port; Qingdao port
★Delivery time: According to customer’s demand or two sides negotiate
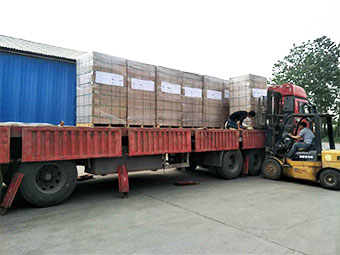
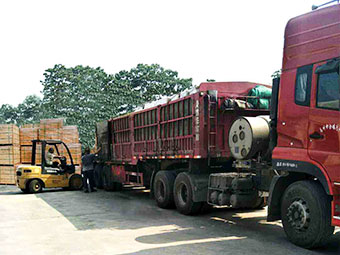
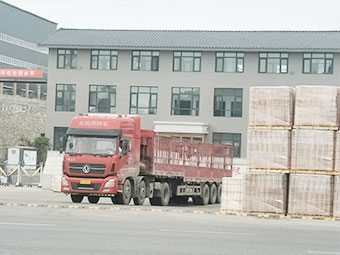
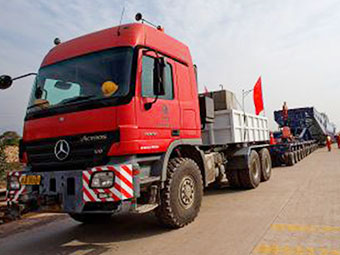
We provide you
★Timely response: Timely response to your inquiry within 24 hours and provide solution.
★Competitive Price: Make the products competitive in your market.
★Free sample: Free sample are offered, trial order are accepted for quality evaluation.
★Strict quality control: We set Quality Management System, from the raw material to finished products, produce high quality products according to chemical & physical specifications strictly to satisfy customers’ needs.
★Fast delivery time: Within 3-30 days according to your quantity after receiving your advance payment.
★ Professional services: Provide pictures from order to delivery. Inspect report by our country’s designated authority and oversea services if necessary.
We are here for you!
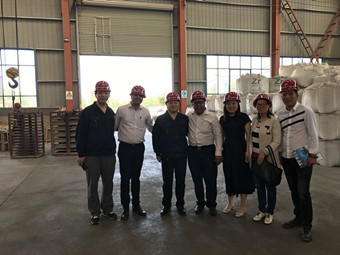
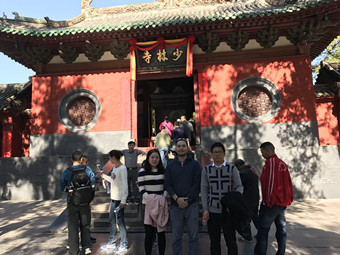
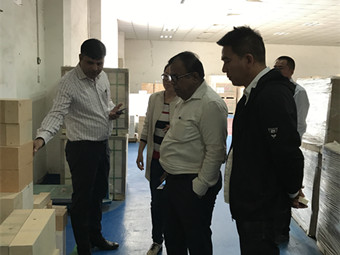
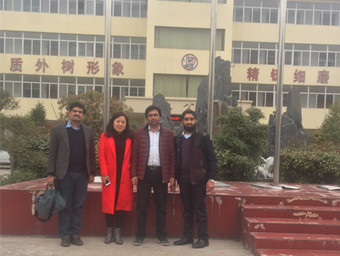
Certification: (ISO 9001:2015)
Please Feel free to give your inquiry in the form below. We will reply you in 24 hours..