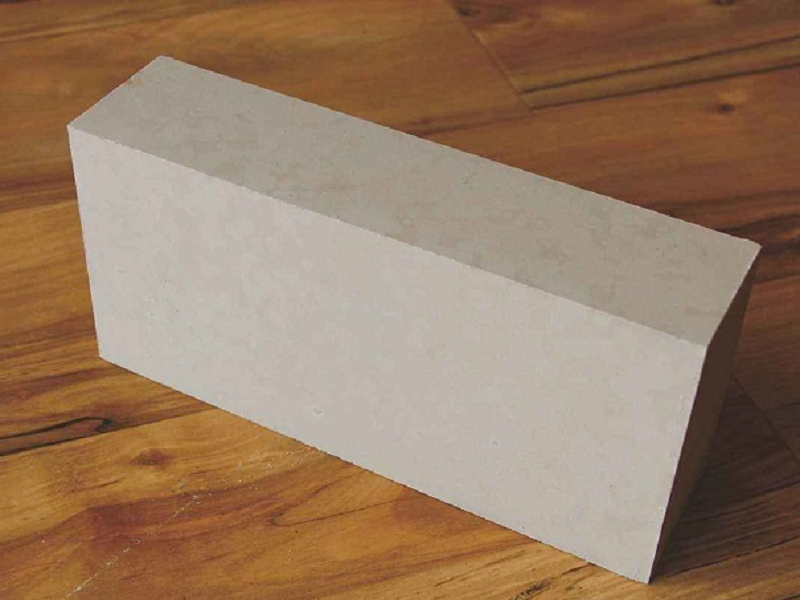
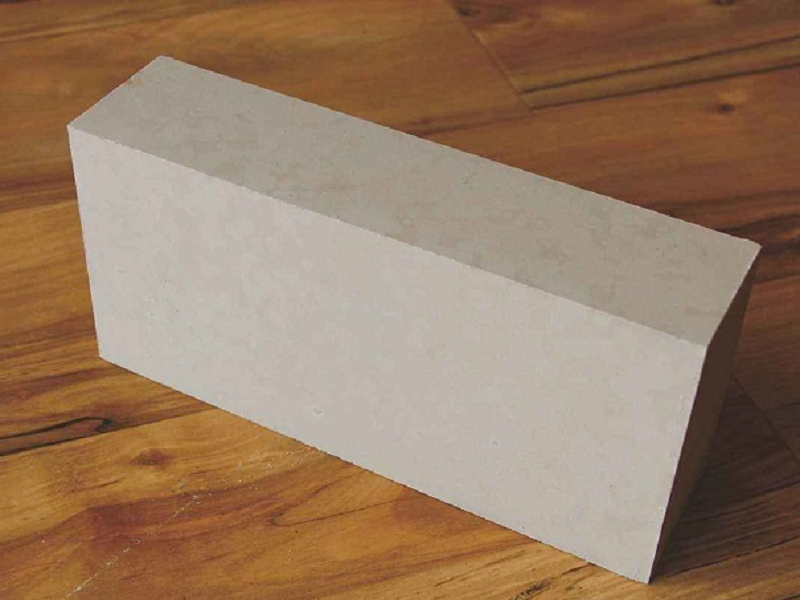
Refractory zircon brick
Model Number: hongtai
Certification:
Minimum Order Quantity:
Refractory High-pure zircon bricks
Pure zircon brick is a zircon-based crystal phase, referred to as high zirconium brick, and is one of the important types of zirconium-containing refractories.
1. Production of pure zircon bricks
(1) Raw material processing. The raw material of the zircon brick is a selected zircon ore, referred to as zircon sand. The mass fraction containing zircon is about 90%.
The zircon concentrate sand has a fine particle size and is single, generally 0.1-0.2 mm. It is not suitable to directly make refractory bricks. In order to obtain pure zircon refractory bricks with coarse particles, it is usually pre-calcined or high-temperature melted to form zircon clinker agglomerates. When calcining the clinker, a part of the concentrate sand is first ground into a fine powder, mixed with another part of the concentrate sand, and bonded with a temporary organic binder to form a ball or a blank, at 1500-1700 degrees (lower than the zircon decomposition temperature). Calcined into dense agglomerates. If an alkali metal oxide or a mineralizer such as MgO or GaO is present, it can be calcined at a lower temperature of 1050 degrees or more. Zircon sands shrink from 900 degrees when calcined, tends to shrink when it reaches about 1350 degrees, and then expands, and then shrinks sharply after 1700 degrees. The zircon concentrate sand mass is improved in compactness after calcination, and the bulk density can reach 3.5g/cm3 or more.
If pure zircon products are produced from fine powder, the concentrate sand can be directly calcined at 1450 degrees, loosened by quenching, and then ground.
(2) Production of high zirconium bricks. For the production of pure zircon products, temporary binders such as sulfite pulp waste liquid, dextrin and lignin may be used, and ethyl silicate, calcium alkylate and phosphoric acid, and water glass may also be used. If a plastic refractory clay is used as a binder, the product is easy to form and sinter, but it tends to cause a decrease in the refractoriness and volume stability of the product. Especially when the amount of clay added to the ingredients is high, the effect is particularly significant.
In order to promote the sintering of pure zircon products, a small amount of CaO, Ca(OH)2, MgO or MgF2 and other mineralizers are often added to the ingredients. This additive promotes the decomposition of ZrO2•SiO2 at high temperatures, forms a ZrO2 solid solution with ZrO2 and enters the glass phase, thereby promoting sintering.
When it is formulated with pure zircon, in order to ensure the good properties and precise shape of the product, the particle size, the amount of the binder and the amount of the admixture must be precisely matched. For articles containing coarse particles of all levels. Multi-stage particle batching is required, and the specific surface area and amount of the fine powder should be higher than that of the ordinary refractory brick to facilitate the formation of a dense green body and to facilitate sintering. If the body consists entirely of fine particles, the maximum particle size of the fine powder is usually below 44 microns, with a few micrometers being the majority. When molding, according to the requirements of the bulk density of the product, ordinary products are generally formed by the method of squeezing mud and dry pressing; the dense ones are mostly cast by mud; the high-density is commonly used for mud casting and isostatic pressing. The various components in the furnish should correspond to the forming method. Pure zircon products must be fired at higher temperatures, and higher density products require higher temperatures. According to the nature and content of the fine powder in the green body and the type and quantity of the mineralizer, the highest firing temperature is generally about 1700 degrees, which should be controlled at a temperature at which the sintered surface of the green body does not undergo significant deformation, and is in contact with the holding time. correspond.
Refractory High-pure zircon bricks Physical and chemical index
Production capacity: Our factory actively response to government environmental protection policy, we designed and built the fully automatic controlled high temperature gas tunnel kiln (1700℃), and got capacity of annual output 70,000 tons of high quality refractory products.
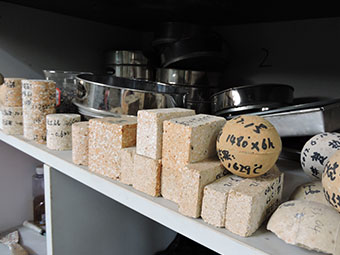
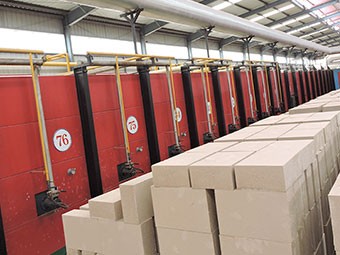
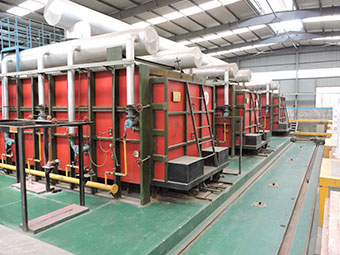
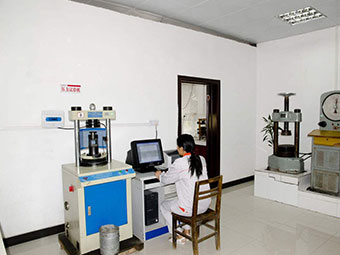
Packing details:
★Bricks: Fumigated wooden pallet with log paperboard covered and stainless steel band strapping, the whole outside is wrapped with thermoplastic film. Or carton packaging.
★Wooden pallet size: usually 92*92cm (standard brick)
★Castable: Ton bag with rain film and 25kg bags inside
★Or according to customer’s requirements
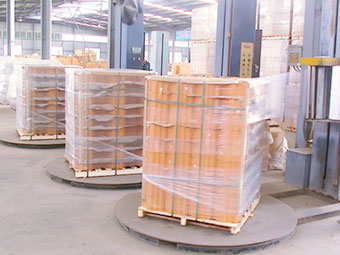
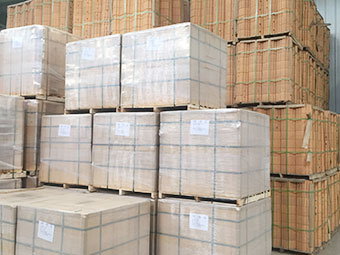
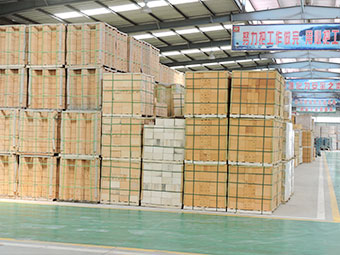
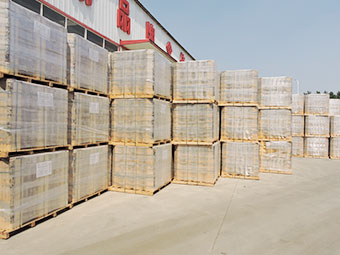
Transportation
★Port of dispatch: Tianjin port; Qingdao port
★Delivery time: According to customer’s demand or two sides negotiate
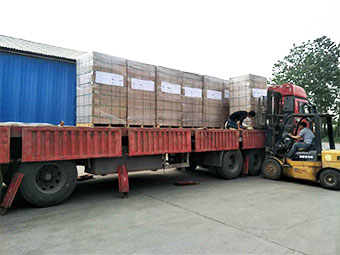
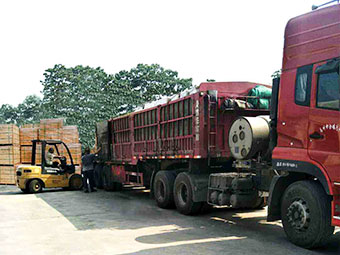
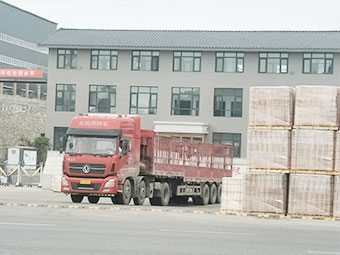
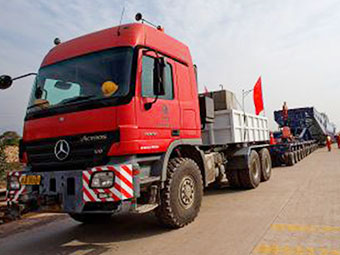
We provide you
★Timely response: Timely response to your inquiry within 24 hours and provide solution.
★Competitive Price: Make the products competitive in your market.
★Free sample: Free sample are offered, trial order are accepted for quality evaluation.
★Strict quality control: We set Quality Management System, from the raw material to finished products, produce high quality products according to chemical & physical specifications strictly to satisfy customers’ needs.
★Fast delivery time: Within 3-30 days according to your quantity after receiving your advance payment.
★ Professional services: Provide pictures from order to delivery. Inspect report by our country’s designated authority and oversea services if necessary.
We are here for you!
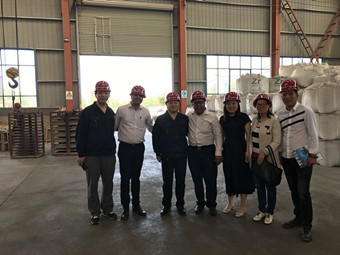
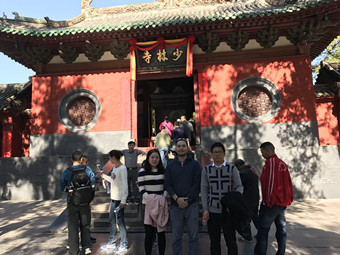
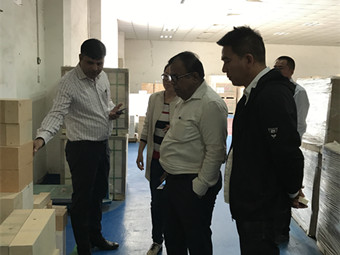
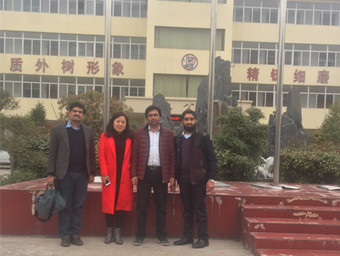
Certification: (ISO 9001:2015)
Please Feel free to give your inquiry in the form below. We will reply you in 24 hours..